数控铣削加工的特点和操作要点
数控铣削方向的选择
影响到切削的起始和完成特性的因素是,铣削时工件顺着或相对刀具旋转方向进给。顺铣是机床、夹具和工件的首选方法。但如果将道具推入工件会无规则增加进给量,由此导致切削厚度过大引起崩刀,这时要选择逆铣。另外当加工余量很多时也选择逆铣。
数控铣削刀具的直径和位置
机床的有效功率和工件宽度是选择铣刀直径的基础,进行面铣时,直接决定铣刀直径的是工件的铣削宽度。一般情况下铣刀直径比工件宽度大,如此才可以保证适当的切削刃负载和良好的切屑形成。理想状况下铣刀的定位要稍微偏离中心,这时刀片形成的切口很小,刀片的进入和退出能够避免出现冲击载荷以及切削,若将刀具完全定位到中心,当切削刃进人或退出切口的时候,大小平均的径向力会在方向上一直变化,机床主轴会出现振动,刀片也可能破碎,表面质量会很差。铣刀对于工件的位置,走刀以及刀齿的接触情况对是否可以完成工序有很大影响。
数控铣削刀具进入和退出条件
每次当一个铣刀刀片进入切口时,切削刃是否会遭受到冲击载荷影响取决于切屑截面、工件材料和切屑类型。铣削过程能不能顺利进行,和切削刃与工件材料之间最初接触和最终接触的类型有很大关系。
这时刀具中心线位于工件宽度之外,刀片切入的时候最外端的刀尖会受到很强的碰撞,表明刀具最敏感的部位容易受到初始的冲击载荷影响。刀片会离开切口只是保持刀尖接触,这表明切削力能完全施加到刀片的外端,直至刀片突然脱离工件,也就是冲击卸载力。
2、铣刀直径比工件宽度稍大
这个时候,工件边缘和刀具的中心线处于同一条直线。当切屑厚度处于最大值刀片会离开切口,在刀片切入和切出时,冲击载荷会非常高。
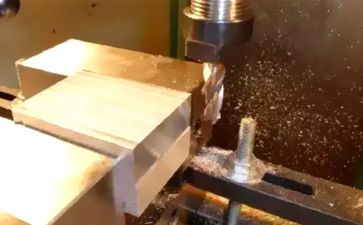
超精度、小批量、工艺复杂都是加工中心铣削加工时的特点,选用切削油的时候要选用专用的加工中心切削油。
数控铣削加工是数控加工中心设备之一,数控铣床在更换工件时只需调用存储于数控装置中的加工程序、装夹工具和调整刀具数据,无需使用专用夹具这些专用工艺设备,极大程度上使生产周期缩短了。加工中心的主轴转速和进给速度均采用无级变速,对选择最佳切削用量很有利,能够完成面铣、方肩铣、仿形铣削、型腔铣削、槽铣、车铣、螺纹铣削、插铣、坡走铣等操作。这里简单介绍下数控铣削加工的特点和操作要点:
1、工件宽度大于或等于铣刀直径
加工中心专用切削油有良好的极压抗磨性能以及良好的通用性,能显著提高加工精度,可以加工各种复杂工艺。此外使用专用切削油还能延长设备以及道具的寿命,防止机台生锈起黄袍。
本文仅代表作者观点,不代表本站立场。
本文系作者授权发表,未经许可,不得转载。
来源:常州市兰生职业培训学校
本文地址:https://www.cnc-school.com/article_1334.htm
- 上一篇:数控铣加工与数控加工中心的区别
- 下一篇:数控铣削加工条件的设定